HDG, BZP and A2/A4 Stainless – What’s the difference?
06 February 2018
You’ll find there are three common fixing finishes on the market. Those are:
- BZP - Bright Zinc Plated
- HDG - Hot Dip Galvanised
- Stainless Steel (A2 and A4)
As you’re probably thinking, each surface finish has its benefits and best use installations so in our article below we break each down and explain the main differentiators between them and you’ll come away understanding exactly which one you need.
Remember, we at VJ Technology have been anchoring ourselves and the No.1 impartial supply-chain partner to the construction and infrastructure sector for over 30 years, so our technical and sales team come with a wealth of knowledge to help you every step of the way with your construction project. View our catalogue online or get in touch with our sales team on 01233 652 550. Please don't hesitate to get in touch with us if you have any questions or concerns about any of the information below.
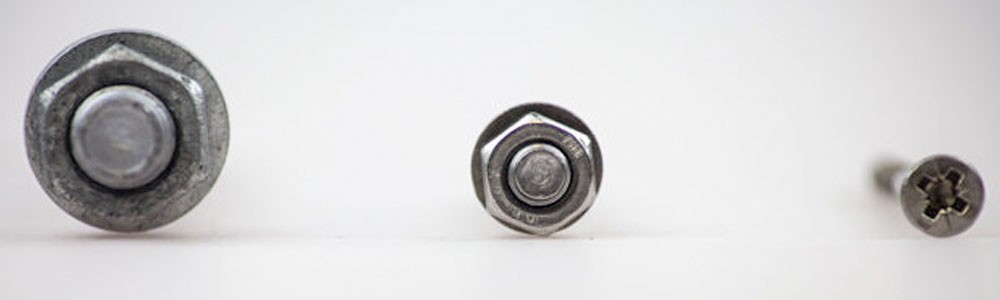
Indoor applications? Think BZP – Bright Zinc Plated:
Bright Zinc Plating tends to be the most popular finish for fixing products. A very thin layer of Zinc is applied to the fixing by way of an electrical current during the manufacturing process and once cured, this layer of zinc acts as protection to the fixing preventing any rusting and oxidisation. Given the layer is ‘thin’, BZP products are best used for indoor applications only as if they’re exposed to all-year-round elements, the Zinc layer won’t hold up and oxidisation will start to occur.
So if your project is indoors-only, this is our recommended fixing finish. We stock plenty of Mechanical Anchors Resin Fixings Self Drilling Screws Bolts, Nuts Bolts & Washers all available in BZP finish.
Outdoor project? Consider HDG - (Hot Dip Galvanised):
Hot Dip Galvanising (HDG) is the process of dipping products in molten zinc, which immediately begins to bond with the surface layer to provide durable protection. More often than not, this is a preferred way of achieving an element-resistant finish due to the cost-effectiveness and low maintenance levels after installation. HDG products benefit from long life, reliability, toughness and low maintenance.
However, it is important to remember that when cutting a galvanised product, you will likely cut through the protective layer into the unprotected metal. An easy way to overcome this is using zinc galvanising spray, which provides protection to the exposed area.
You’ll find many products on our website finished by HDG, such as wall brackets, cantilever beams, clamps.
Need extra strength? Opt for Stainless Steel - A2 & A4
For general use, Stainless Steel is a steel oxide with a minimum of 10.5% Chromium content. This Chromium adds a protective capacity to the steel, helping it to resist corrosion. Whilst both Stainless Steel and HDG fixings are great options for rust protection, Stainless Steel comes out on top offering greater corrosion protection over HDG and remains the
A2 Stainless (Type 304):
The most popular choice for the production of construction fixings and fasteners is A2 Stainless. It contains 18% Chromium, and 8% Nickel. While suitable for applications in an outdoor environment, A2 stainless can discolour over time. It is resistant to sterilising solutions and man-made chemicals and is used extensively in the food production/preparation industry.
A4 Stainless (Type 316):
This variant contains the same 18% chromium and 8% nickel found in A2 but it also includes 3% molybdenum which provides extra resistance and it’s this that amounts to the name 'A4 Stainless (Type 316)' grade. This variant is commonly found in marine and chemical applications thanks to its long lifespan and extra resilience to corrosion and tarnishing.
To summarise
BZP - Bright Zinc Plated
The Positives:
- Visually appealing.
- Versatile to work with.
- Great value for money.
The Drawbacks:
- Limited to use for indoor applications only due to low corrosion resistance.
HDG - Hot Dipped Galvanised
The Positives:
- Long-lasting and low maintenance.
- Greater corrosion protection due to the thicker plating.
- Whilst more expensive than BZP, it's still a very cost-effective option.
The Drawbacks:
- There are other finishes with a greater visual appearance.
A2 Stainless Steel
The Positives:
- Has great levels of strength and corrosion resistance.
- Looks great.
The Drawbacks:
- Higher upfront costs, but will pay for itself over time by reducing maintenance and replacement costs.
- Can be a harder finish to work with when installing due to its strength.
A4 Stainless Steel
The Positives:
- Very minimal risk of tarnishing over time.
- Looks great.
- Marine-grade strength.
The Drawbacks:
- Higher upfront costs, but will pay for itself over time by reducing maintenance and replacement costs.
- Supply can be limited due to its very selective requirement applications.